Sponge vertical foaming process vertical continuous production technology
Vertical foam process vertical continuous production of sponge technology, is the UK Hymon national title Limited in the 1980s developed and patented new technology. The vertical method has attracted the attention of polyurethane industry and achieved rapid development because of its outstanding advantages.
(1) sponge vertical foaming machine equipment investment small footprint, no top skin product rate is high, simple operation, sponge vertical foaming in the production process because of small flow changes formula is much easier than horizontal foaming. The density distribution is uniform and the diameter of the round foam is 1.5 meters.(2) Round bubble has high production technology requirements, 10 density of the machine should be made small changes, otherwise the bubble body is easy to crack after dozens of minutes of foaming, better in winter, the company adds powder up to 80%, high load and high rebound can be sent, can not send slow rebound and super soft. Anti super soft can, more than 40 density is not good hair.
(3) The mixing head is the key part of the good or bad foam structure, and also the most troublesome part for the equipment manufacturers and users. Especially for the round bubble, some manufacturers adopt the pressure air injection speed adjustment structure, which can make the product have several or more bubbles. Without the pressure air injection, the structure is not so ideal if the bubbles are less. (For example, flocking sponge is mostly imported)
(4) The formula and design of the round bubble is not exactly the same as that of the horizontal bubble, mainly amine tin silicone oil. In the foaming process, there is pressure shrinkage, splitting, arc cracking, horizontal cracking, peeling. If the flow is correct, it is basically the problem of the formula, and sometimes the same failure occurs in fake raw materials.
Equipment configuration and matters needing attention of sponge vertical foaming machine:
① The area is greatly reduced, only 600 square meters;② the total flow of material is reduced to 20, 40kg/min;
(3) The same equipment can produce round foam block and rectangular foam block, only need to replace some parts, can be produced alternately;
(4) The size of foam block is regular, and the waste material can be reduced to 4%~6%;
(5) In the same cross section, the foam physical property distribution is uniform;
⑥ Reduce the loss of start/stop, the length of defective products in lm, this process is suitable for the annual output of 500~ 4000T small and medium-sized factories. At the same time, low investment cost, labor saving.
The vertical process is composed of several steps, such as raw material storage, measurement, mixing, input, foaming d, curing, foam lifting, cutting and foam transportation.
The specific operation is to first measure all kinds of chemical: raw materials by the metering pump, feeding into the mixing head: closed, and then into the foaming tray, foaming. The foaming process is carried out in the bag surrounded by polyethylene film. With the increase of the cross-sectional area, the foaming direction is in the horizontal direction along the long axis with bubbles. In the foaming chamber, the density gradually decreases from bottom to top, with a density gradient. Due to the effect of gravity, there is no backmixing between the foaming material layer and layer. The influence of gravity is equal on the same cross section, so the physical properties are basically the same on the same cross section. After foaming, the foam body enters the curing section, and there is a heating cylinder in the curing section. The heating cylinder is surrounded by an insulation layer, and the heating promotes the rapid curing of the foam. Before foaming, preheat the heating cylinder to about 65°C. After normal operation, the heating can be stopped and the temperature can be maintained by foaming heat.
After aging, the foam enters the lifting section, which is composed of a conveyor belt composed of slats. There are small needles (needle length about 1.SCM) on the slats. The small needles penetrate into the outer skin of the foam and rise continuously with the foam, which is surrounded by 10 conveyor strips to form a circle. There are many factors affecting the process of vertical PU block foam, but the most important thing is to master the balance and stability of the formula during the operation of foaming machine. It should be observed at any time to understand the raw material temperature, curing temperature, ambient temperature, flow rate, pressure, mixing factors (mixing speed, mixing head pressure, air injection amount), catalyst dosage, etc., and adjusted and controlled in the foaming process in time to produce excellent products.
Some abnormal phenomena often appear in the running process of vertical foaming machine, and measures should be taken to solve them in time in order to maintain normal production.
The most common ones are the following.
(1) the bubble "tightening" or contraction: when foaming, when the bubble rises to the highest point, the bubble hole bursts, and there is foaming phenomenon, which is normal foaming, if this is not the case, the bubble will "tightening" or closed cell. This reason is mainly due to excessive tin catalyst and fast pore wall of gel. Or too much foam stabilizer, bubble hole is too stable and can not be blown open, resulting in large obturator.(2) Bubble burst: the main reason is that the operation formula is wrong, the calculation pump error, resulting in inaccurate formula, out of control. The lack of tin catalyst and foam stabilizer or the decrease of activity are the main causes of bubble bursting. Other mechanical factors will also cause bubble bursting phenomenon, such as too fine bubble hole, foreign impurities, oil pollution, conveyor belt speed is not stable or fluctuating, the shape and size of polyethylene bag is not appropriate, will lead to bubble bursting.
(3) Foam slide: This happens when the pin-board conveyor belt can't hold the foam, usually when the "starting ring" is removed. The foam stops rising and even falls, and marks can be seen on the surface of the foam. Analysis of the reasons include too long rising time, too low temperature of curing section, foam did not fill the whole section, foam closed hole high, "tightening", conveyor belt speed too fast or improper installation will cause foam sliding phenomenon.
(4) compression line: it refers to the obvious white interface in the foam block, and the white line is obvious on the cut cross section. The foam strength on the white line is very poor and belongs to the unqualified product. This white line is called a compression line. This occurs if the conveyor is too slow, either by reducing the amount of spit to keep the conveyor at the same speed, or by gradually increasing the speed of the conveyor to eliminate such compression lines. The way to eliminate the compression line is to estimate how far the foam in the full rise into the curing section, if it is just into the curing section of the full rise, it is best to only increase the speed of the conveyor belt; If the whole rise has entered the curing section far, it is best to reduce the amount of spit, keep the conveyor belt speed unchanged.
Latest News
Contact Us
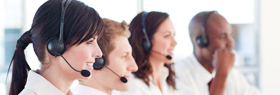
Name: Dylane shi
E-mail: [email protected]
QQ: 627812212
WeChat: qd627812212
Whatsapp: +8618061811323
Add: Qingdao City, Shandong